In the production field of seamless titanium alloy tubes, rolling, stretching, and spinning are the three main and distinctive production methods. These methods not only meet the demand for Titanium Tube in different fields, but also promote the rapid development of related industries such as low altitude economy.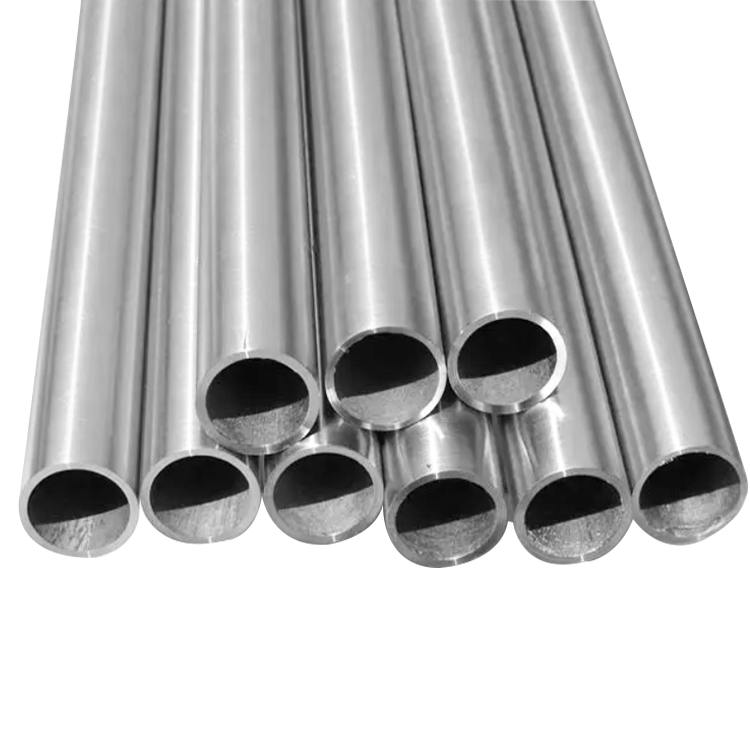
Firstly, let's delve into the traditional and important production method of pipe rolling. Rolling is the preferred method for producing precision, thin-walled tubes of Titanium Materials and titanium alloys. Its significant advantage lies in the ability to produce high-strength, low plasticity metal pipes, which have a wide range of applications in high-end fields such as aerospace and medical equipment. In addition, the production cycle of rolling methods is relatively short and can quickly respond to market demand. At the same time, the rolled pipes have precise dimensions and high smoothness, meeting customers' high requirements for product quality. However, there are also some challenges with the rolling method. Due to the complexity and high investment of rolling equipment, the requirements for tools are also quite strict, which to some extent increases production costs and difficulties.
Next, let's take a look at the production method of stretch pipes. The stretching method is known for its high flexibility and easy replacement of molds. Compared with rolling, stretching equipment has relatively lower investment and manufacturing difficulty, making it more suitable for small and medium-sized production. In addition, the stretching method is very suitable for producing special-shaped pipes and bars, providing the market with more diversified product choices. However, the stretching process faces certain difficulties in producing low plasticity, high-strength metal pipes, which limits its application in certain specific fields.
Finally, let's explore the production method of spinning pipes. The spinning method is highly favored for its small equipment shape, light weight, and low investment. Compared with rolling and stretching, spinning method can produce large-diameter thin-walled pipes that exceed the capacity of existing rolling and stretching equipment, which is of great significance for meeting the market demand for large-diameter and thin-walled pipes. However, there are also some challenges in the spinning process. Due to the significant unevenness of deformation, high requirements are placed on the inner hole size and surface quality of the pipe blank, which may pose certain difficulties in large-scale production. Therefore, when using the spinning method, it is necessary to strictly control each link in the production process to ensure product quality.
In summary, the diversified production methods of Seamless Titanium Pipe have their own advantages and disadvantages. When choosing a production method, it is necessary to weigh the specific application scenarios and requirements. Meanwhile, with the continuous advancement of technology and the expansion of the market, the production methods of titanium alloy seamless pipes will also be constantly innovated and improved to meet more diverse and high-performance needs. In the future low altitude economy and other fields, titanium alloy seamless pipes will continue to play an important role, providing strong support for the development of related industries.