In the modern pharmaceutical industry, the selection of materials is directly related to drug quality, production efficiency, and equipment lifespan. titanium alloy is becoming the preferred material for pharmaceutical equipment manufacturing due to its unique performance advantages.
Excellent characteristics of titanium alloy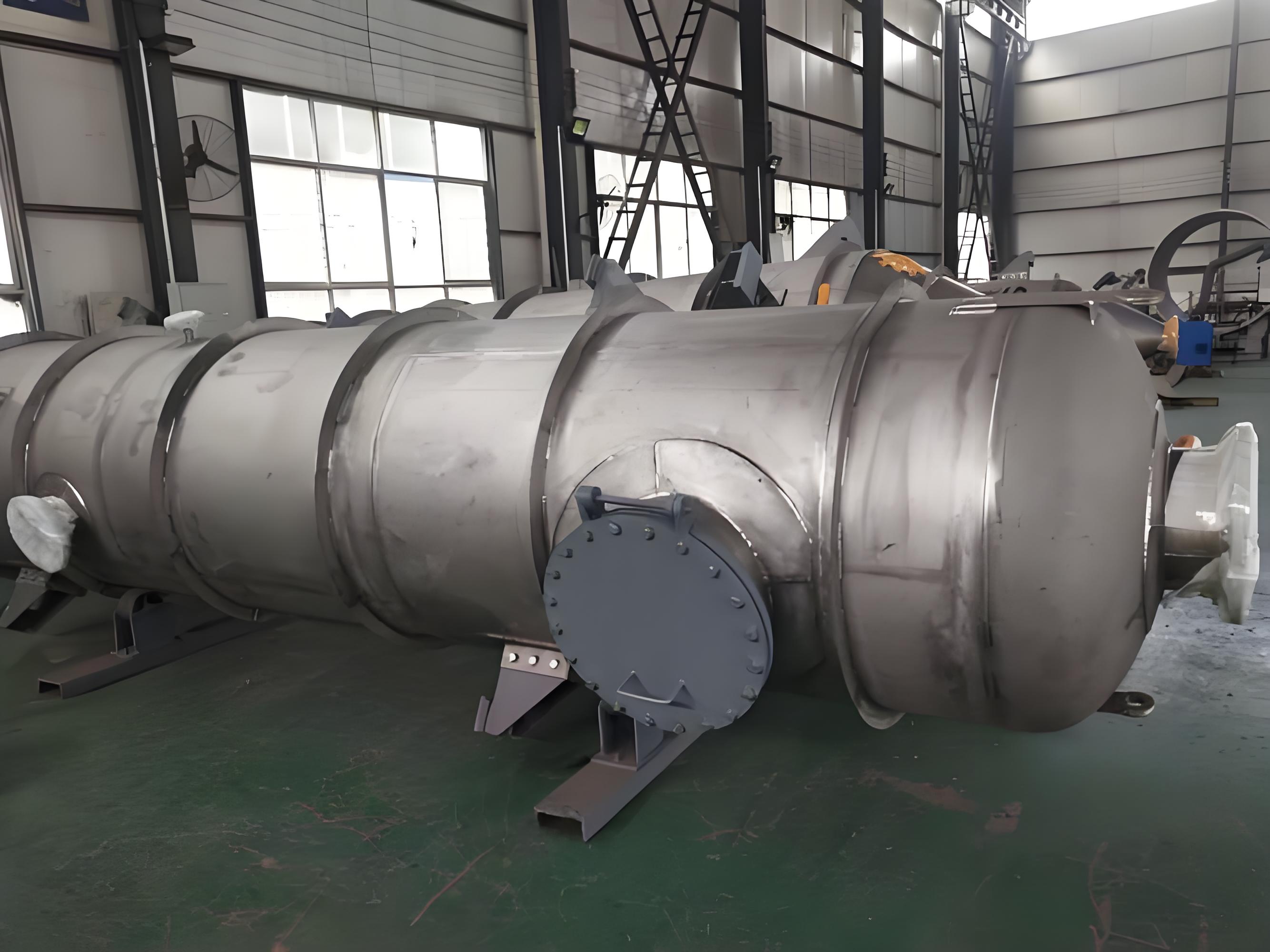
Titanium alloy has three core advantages: firstly, unparalleled biocompatibility, fully complying with ISO 10993 medical device standards, ensuring that harmful substances are not introduced during the drug production process; Secondly, it has excellent corrosion resistance, showing outstanding performance in strong acid, strong alkali, and organic solvent environments, with an annual corrosion rate of less than 0.01mm; The third is excellent mechanical performance. TC4 titanium alloy has a strength 30% higher than pure titanium, making it particularly suitable for manufacturing high-speed centrifuge and agitator components.
Typical application case analysis
In the production of vitamin B1, traditional stainless steel equipment will experience corrosion perforation after only one year of use in hydrochloric acid thiamine medium. After switching to equipment such as spiral feeders and cyclone separators made of titanium alloy, not only did the product qualification rate increase to 100%, but the equipment also operated continuously for 7 years without any signs of corrosion, and the investment return cycle was shortened to 3 months.
The high-temperature gulonic acid environment during the production process of vitamin C is extremely corrosive to equipment. After using TC4 titanium alloy to cast impellers and Titanium Tube heat exchangers, the equipment remained intact even after running for more than 20000 hours, greatly reducing maintenance costs and production interruption risks.
Solutions in the production of special drugs
The production of antibiotics faces serious corrosion problems caused by chlorine containing organic solvents. Taking chloramphenicol production as an example, the use of TA10 titanium alloy equipment in the distillation process has extended the service life from 1 year to 10 years, while avoiding drug contamination caused by equipment corrosion.
In the production of the anesthetic procaine, the combination of titanium steel composite plate reaction kettle and titanium bubble tube has successfully solved the corrosion problem caused by strong acid nitration reaction. The migration of metal ions is controlled below 0.1 μ g/cm ², fully meeting the purity requirements of the drug.
Economic benefits and industry prospects
From an economic perspective, although the initial investment of Titanium Equipment is relatively high, its ultra long service life (15-20 years) and extremely low maintenance requirements reduce the overall cost by more than 40% compared to traditional stainless steel equipment. With the development of 3D printing technology, the manufacturing cost of complex titanium alloy components is rapidly decreasing, which will further promote the application of titanium alloys in the pharmaceutical industry. In the future, with the development of pharmaceutical technology towards higher efficiency and precision, Titanium Materials will undoubtedly play a more important role in the field of high-end pharmaceutical equipment. Pharmaceutical companies should fully recognize the technological advantages of titanium alloys and prioritize the use of titanium alloy equipment in key production processes to improve product quality and production efficiency.